ImGo – cyfryzacja obiegu informacji w zarządzaniu zasobami
Połączenie najlepszych praktyk w obszarze narzędzi, procesów i ludzi, pozwalające na przełożenie celów i planów dotyczących zasobów przedsiębiorstwa na codzienne
zadania.
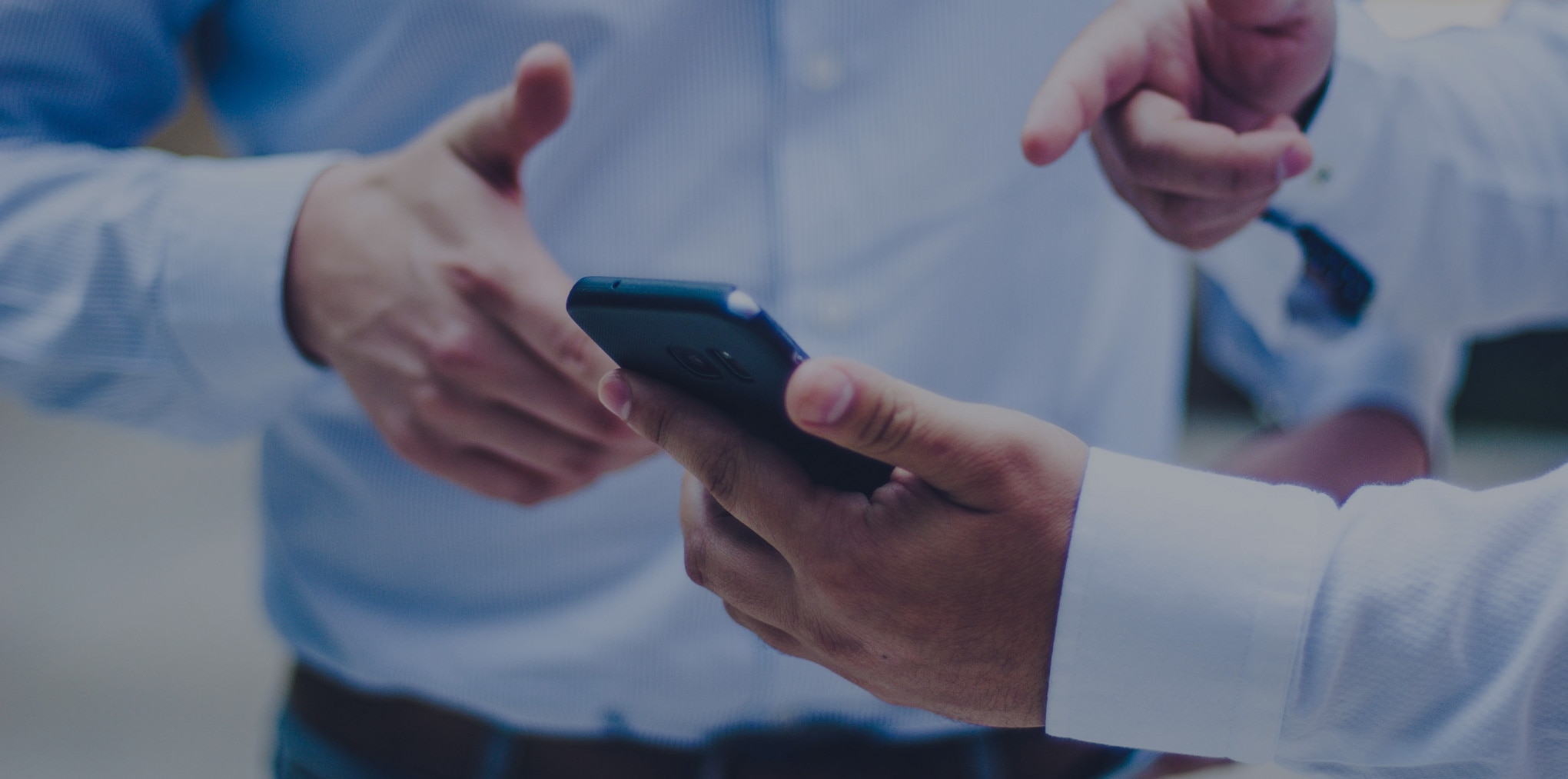
ImGo to system cyfrowego, mobilnego obiegu informacji i raportowania dla wsparcia procesów zarządzania i nadzoru nad obiektami, pracownikami oraz zasobami organizacji.
Główne funkcjonalności
Kompletny zestaw funkcji do efektywnego zarządzania i rejestrowania procesów operacyjnych oraz przepływu materiałów w zakładach przemysłowych
Myślisz o rozwoju w kierunku monitoringu maszyn? Wypróbuj system ImProdis MES już teraz!
Zestaw startowy z monitoringiem 5 maszyn już od 21 000 PLN rocznie
Poznaj szczegóły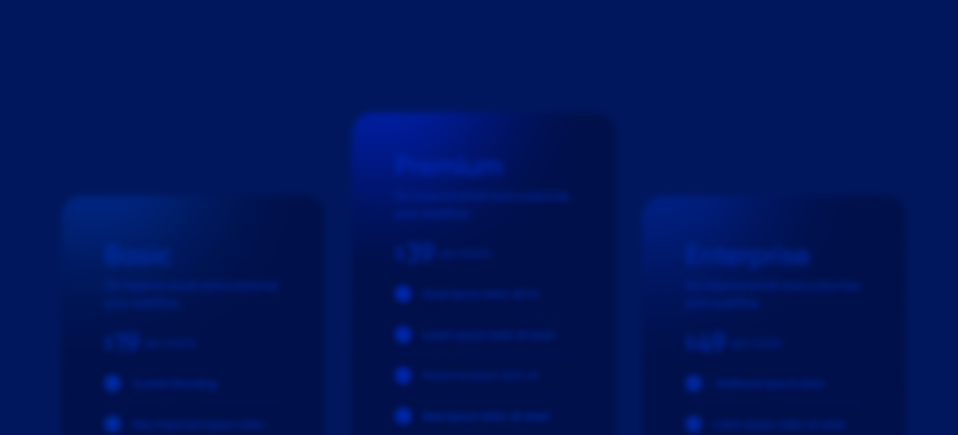
Jak działamy jako ImFactory AVEVA MES Competence Center CEE
Artykuły
Chcesz dowiedzieć się więcej? W naszej Bazie Wiedzy znajdziesz artykuły i webinary przygotowane przez ekspertów, które pozwolą Ci poszerzyć wiedzę.
FAQ
Zobacz, o co najczęściej pytają Klienci zainteresowani systemem ImGo i poszerz swoją wiedzę w tym temacie.
ImGo to system cyfrowego, mobilnego obiegu informacji i raportowania dla wsparcia procesów zarządzania i nadzoru nad obiektami, pracownikami oraz zasobami organizacji.
Główną korzyścią z zastosowania ImGo jest skuteczna transformacja cyfrowa firmy na poziomie zastąpienia papieru i arkusza kalkulacyjnego przez mobilne formularze oraz system bazodanowy.
System ImGo jest systemem bazodanowym, więc może się integrować z każdym innym systemem tego typu. Zarówno jako dostawca i odbiorca danych. Częstą praktyką jest wdrażanie systemu ImGo jako mobilnego interfejsu do wprowadzania informacji do istniejącego w firmie systemu, który takiej funkcjonalności nie posiada
Projekt wdrożenia systemu ImGo, tak jak każdy inny projekt, rozpoczynamy od określenia na jakie problemy, potrzeby czy wyzwania ma odpowiedzieć system i w jakim stopniu. Dopiero po ustaleniu tych kwestii możemy rozpocząć prace związane określeniem głównych użytkowników, interesariuszy projektu czy przeprowadzenia inwentaryzacji posiadanych maszyn i systemów, a także specyfikowania konkretnych wymagań. Na tym etapie można zaprosić do pomocy zewnętrznego konsultanta.
Wdrożenie systemu ImGo warto zacząć od przygotowania wersji demonstracyjnej w postaci Proof of Concept lub Proof of Value. Oznacza to wdrożenie systemu w wersji ograniczonej funkcjonalnie lub obszarowo, ale w zakresie, który dowiedzie, że odpowiada on na główne cele projektu. Jest to etap biznesowego uzasadnienia inwestycji, w efekcie którego dostarczane jest tzw. MVP (z ang. Minimal Value Proposition)
Cena systemu ImGo zależy od wielu czynników i może mieścić się w przedziale od kilku tysięcy do nawet kilkudzisięciu tysięcy złotych. Do głównych czynników warunkujących cenę systemu ImGo można zaliczyć liczbę użytkowników, obiektów i formularzy zakres funkcjonalny, sposób licencjonowania (wieczyste lub subskrypcyjne) czy sposób hostowania (lokalnie, w chmurze, hybrydowo).
Pierwsze wdrożenia systemu ImGo miały miejsce w firmach zarządzających rozproszoną strukturą obiektów, czyli w branży wod-kan i ciepłowniczej. Potem pojawiły się implementacje w wielu firmach produkcyjnych m.in. z branży meblarskiej, automotive, spożywczej i innych.
Obsługa powdrożeniowa dzieli się na gwarancyjną oraz pogwarancyjną (serwisową). Niezależnie od okresu, na obsługę powdrożeniową składają się procesy obsługi tzw. SR (z ang. Service Request), które obejmują przygotowywanie poprawek i obejść zgłoszonych błędów, aktualizacje wersji oprogramowania, monitoring wydajności systemu – ogólnie wszystkie zagadnienia związane z zapewnieniem ciągłości funkcjonowania w myśl zapisów SLA. Drugim obsługiwanym strumieniem zgłoszeń są tzw. FR (Functional Request), które polegają na wprowadzeniu ulepszeń, optymalizacji, zmian w konfiguracji czy dodawaniu nowych funkcji lub obszarów – czyli szeroko rozumiana rozbudowa systemu. Dodatkowo konsultanci odwiedzają zakład, w gemba sprawdzają jak system jest wykorzystywany i zbierają feedback bezpośrednio od użytkowników.
Typowe obszary rozwoju systemu ImGo to: • dodanie nowych funkcji, które nie zostały jeszcze zaimplementowane, • rozszerzenie systemu na nowe obszary np. wydziały, które nie zostały jeszcze zdigitalizowane, • integracja z systemami zewnętrznymi, dla których nie ustanowiono do tej pory kanałów komunikacji. Obszary te mogą oczywiście występować w różnych kombinacjach i zakresach.
ImGo zapisuje dane w standardowej bazie Microsoft SQL lub PostgreSQL, do której dostęp jest otwarty dla użytkowników o odpowiednim poziomie uprawnień. Dzięki temu, bez najmniejszego problemu, baza danych ImGo może zostać podłączona jako źródło danych do dowolnego rozwiązania klasy BI, a także innych narzędzi takich jak arkusze Excel, Google Sheet, Minitab czy Statistica.
Umów się na bezpłatną prezentację lub rozmowę na wskazany przez Ciebie temat.
Jak przebiega proces bezpłatnej konsultacji?

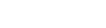
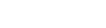
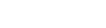
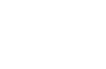
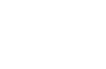
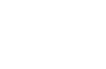
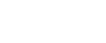
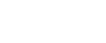
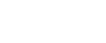
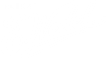
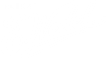
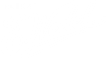



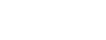
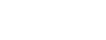
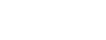



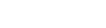
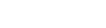
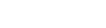
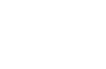
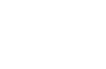
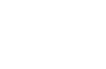
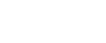
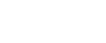
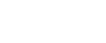
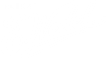
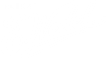
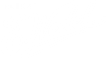



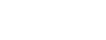
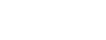
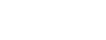



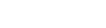
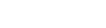
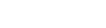
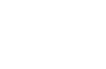
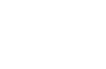
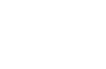
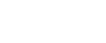
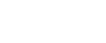
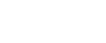
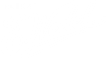
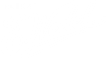
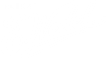



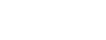
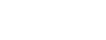
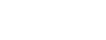



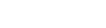
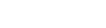
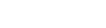
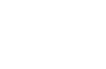
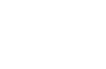
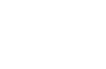
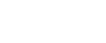
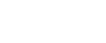
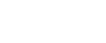
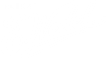
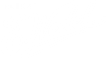
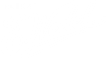



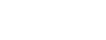
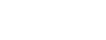
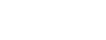